The Evolution of Laser Welding Equipment for Metal Fabricators
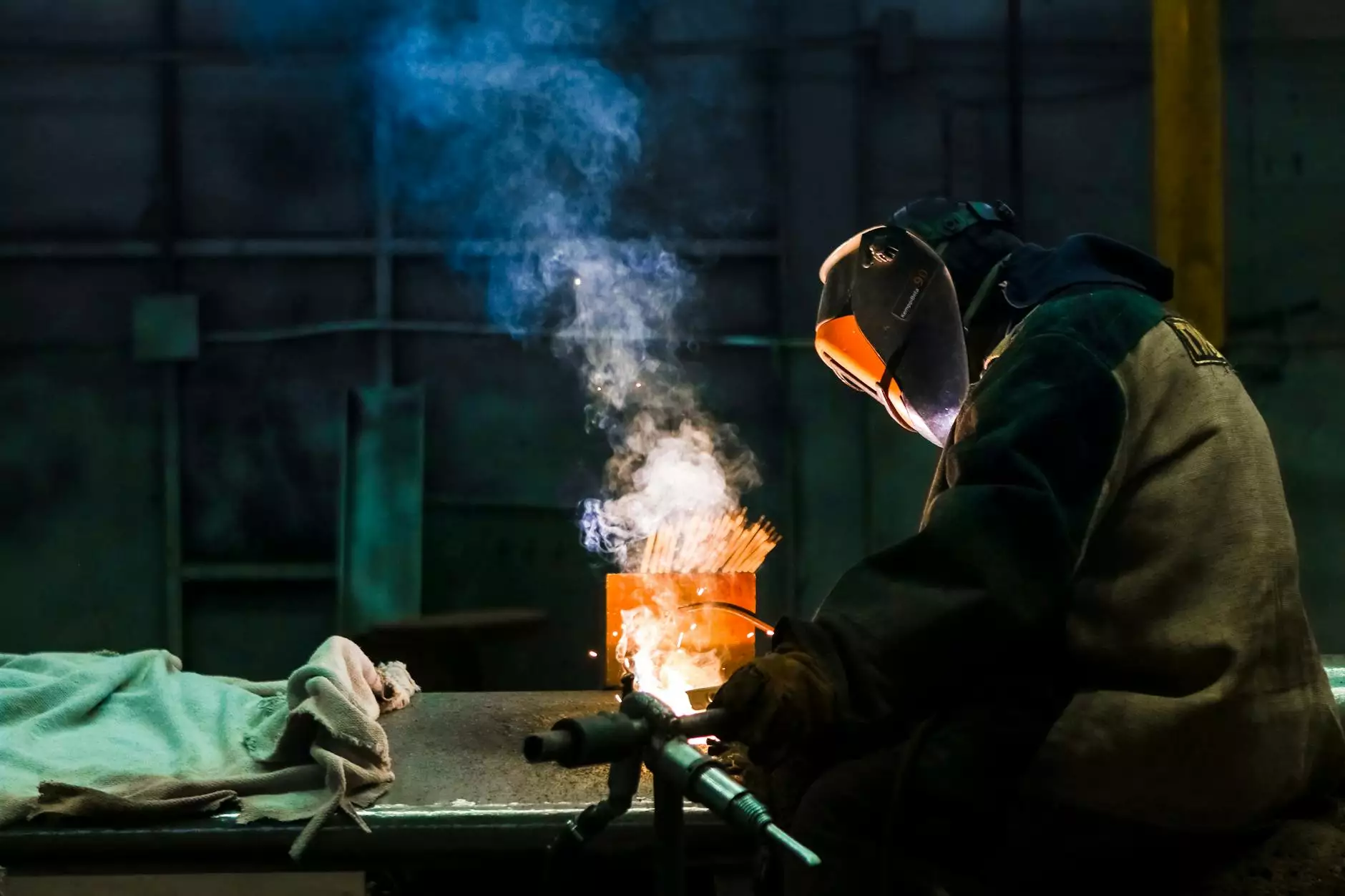
As technology continues to advance at a rapid pace, the field of laser welding equipment has seen remarkable growth and innovation, especially for metal fabricators. The precise and efficient nature of laser welding has revolutionized the way metal fabrication is carried out, paving the way for enhanced productivity and quality. In this article, we'll delve into the latest advancements in laser welding equipment and how it is shaping the future of the metal fabrication industry.
Increased Precision and Efficiency
One of the key advantages of using laser welding equipment is its unmatched precision and efficiency. By harnessing the power of concentrated laser beams, metal fabricators can achieve incredibly precise welds with minimal heat-affected zones. This level of precision not only enhances the overall quality of the welds but also minimizes material wastage, making the process more cost-effective.
Enhanced Productivity and Faster Turnaround Times
With the introduction of advanced laser welding equipment, metal fabricators can significantly improve their productivity levels and reduce turnaround times. Laser welding machines are capable of performing high-speed, automated welds, allowing for quick and efficient processing of metal components. This not only boosts efficiency but also enables metal fabricators to take on larger volumes of work while maintaining consistent quality.
Improved Weld Quality and Strength
Quality control is a top priority for metal fabricators, and laser welding equipment plays a crucial role in ensuring superior weld quality and strength. By producing welds with minimal distortion and defects, laser welding technology helps fabricators achieve structurally sound and aesthetically pleasing results. The high energy density of laser beams enables deep penetration welding, resulting in strong, durable bonds that can withstand rigorous applications.
Advanced Features and Customization Options
Modern laser welding equipment comes equipped with a range of advanced features and customization options to cater to the diverse needs of metal fabricators. From adjustable beam parameters to sophisticated control systems, these machines offer unparalleled flexibility and adaptability in welding various types of metals and components. Additionally, the ability to program and automate welding processes allows fabricators to achieve consistent results with minimal human intervention.
Integration with Industry 4.0 Technologies
As the era of Industry 4.0 takes hold, laser welding equipment is increasingly being integrated with smart technologies to optimize efficiency and connectivity in the manufacturing environment. By leveraging data analytics, IoT sensors, and cloud-based systems, metal fabricators can monitor and control their welding processes in real-time, leading to improved decision-making and predictive maintenance. This seamless integration enhances overall productivity and ensures the highest level of quality in metal fabrication.
Conclusion
In conclusion, laser welding equipment has become an indispensable tool for metal fabricators looking to stay ahead in today's competitive market. With its unmatched precision, efficiency, and quality, laser welding technology offers a myriad of benefits that can elevate the fabrication process to new heights. By embracing the latest advancements in laser welding equipment and leveraging its capabilities, metal fabricators can not only improve their operational efficiency but also achieve superior weld quality that sets them apart from the competition.
Visit dplaser.com to explore our range of cutting-edge laser welding equipment designed to meet the evolving needs of metal fabricators.