Pump Cavitation: Understanding and Preventing Issues in Auto and Farm Equipment
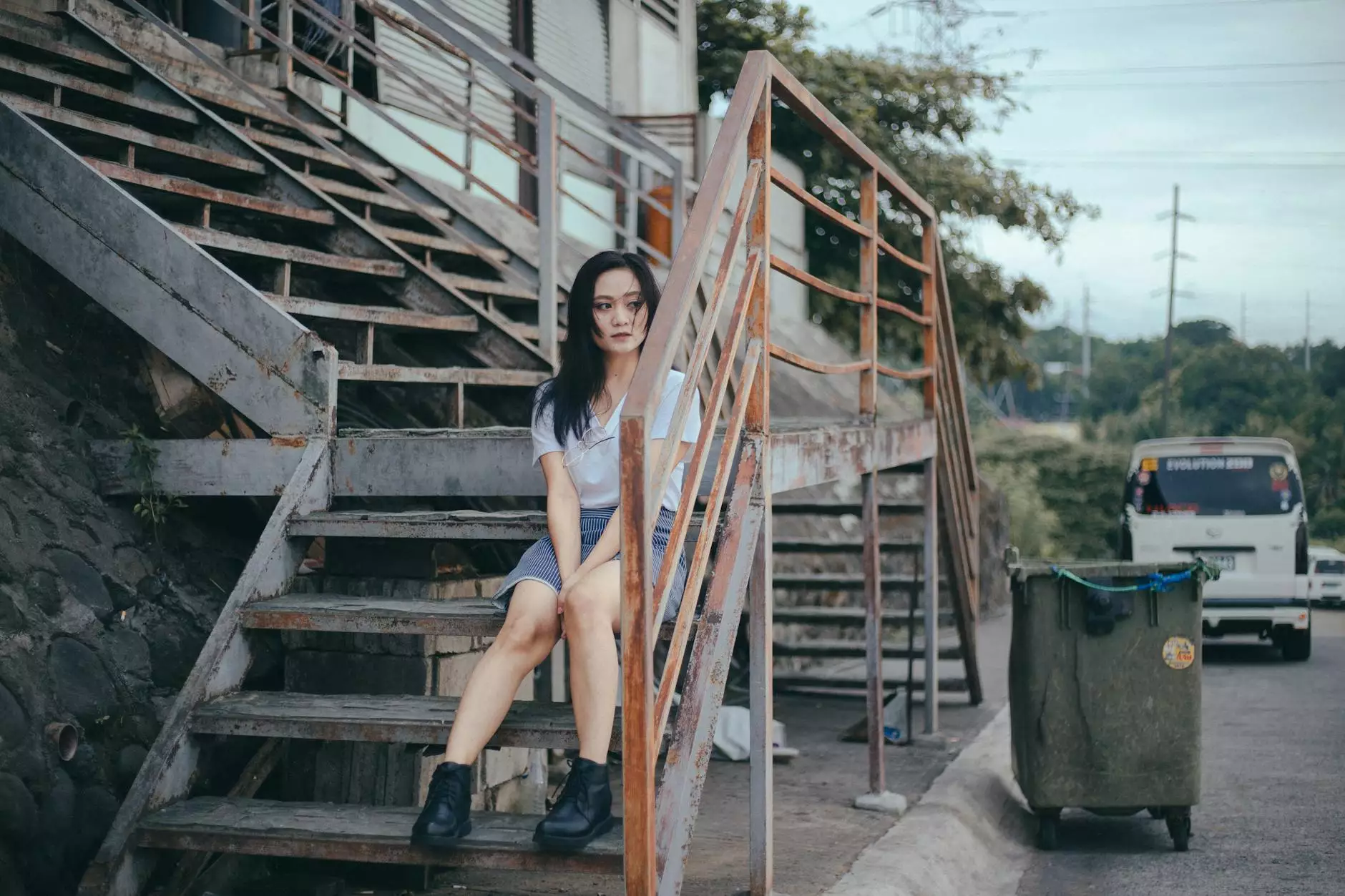
Pump cavitation is a critical issue that affects various industries, particularly in the realms of auto repair, farm equipment repair, and the expertise of structural engineers. In this article, we will delve deep into the phenomenon of pump cavitation, its implications on machinery, and detailed strategies for prevention. Understanding pump cavitation is essential for maintaining the efficiency and longevity of sophisticated mechanical systems.
What is Pump Cavitation?
Pump cavitation occurs when the pressure in a fluid drops below its vapor pressure, causing the liquid to form vapor bubbles. These bubbles can collapse violently when they move into areas of higher pressure, resulting in a phenomenon known as shock waves. This dynamic can severely impact the mechanical integrity of pumps and the systems in which they operate.
The Physics Behind Cavitation
The science of cavitation is rooted in the principles of fluid dynamics. When a pump operates, it generates a pressure drop at the inlet, which can sometimes dip below the vapor pressure of the liquid being pumped. This can be caused by several factors, including:
- High flow rates: Excessive demand on the pump can lead to pressure drops.
- Improper pump selection: Choosing pumps that are not suited for specific applications can create operational issues.
- Temperature variations: Increased temperature can lower the vapor pressure of liquids.
Effects of Pump Cavitation
The consequences of pump cavitation can be detrimental:
- Wear and tear: The implosion of vapor bubbles produces high-energy shock waves, resulting in erosion on the surfaces of the pump.
- Reduced efficiency: Cavitation leads to decreased performance and efficiency of pumping systems.
- Increased operational costs: Poor pump performance can lead to further mechanical issues, requiring additional repairs.
- System failure: In severe cases, cavitation can result in catastrophic pump failure and long downtimes.
Identifying Cavitation Issues
Detecting cavitation early can save significant time and resources. Some common signs of pump cavitation include:
- Strange noises: A distinct rattling or churning sound can indicate that cavitation is occurring.
- Vibration: Excessive vibration levels can suggest a problem with cavitation.
- Fluctuating output: Inconsistent flow rates or pressures can be a sign of cavitation disrupting normal operation.
Preventing Pump Cavitation in Auto Repair and Farm Equipment
Prevention is always more effective than remediation. Here are several strategies that can be employed to minimize or eliminate pump cavitation:
1. Proper Pump Selection
Choosing the right pump for the application is essential. Engineers should assess:
- Flow requirements: Match the pump to the anticipated flow rate.
- Fluid properties: Consider the characteristics of the fluid, including temperature and viscosity.
- System layout: Evaluate the design and layout of the entire system to prevent inlet restrictions.
2. Maintaining Sufficient Net Positive Suction Head (NPSH)
NPSH is crucial for preventing cavitation. Ensuring that the available NPSH exceeds the required NPSH of the pump can mitigate cavitation risks. Achieving a high NPSH involves:
- Reducing pipe friction losses: Utilize properly sized and smooth-walled piping.
- Minimizing elevation differences: Avoid significant vertical lifts from the supply source to the pump inlet.
- Installing an NPSH gauge: This can help monitor levels and manage adjustments accordingly.
3. Regular Maintenance and Inspection
Regular maintenance is vital for every pump. Scheduled inspections can include:
- Checking seals: Ensure that seals are intact to avoid leaks that might introduce air.
- Monitoring temperature: Keep track of operating temperatures to detect abnormal behaviors.
- Inspecting the impeller and casing: Regularly examine these components for wear and tear.
4. Implementing Flow Modifiers
In some cases, flow modifiers can be useful to reduce the risk of cavitation. Options include:
- Flow straighteners: These can help smooth the flow entering the pump.
- Diffusers: Can slow the flow and increase pressure at the pump inlet.
Impact on Structural Engineering
Cavitation does not only affect pumps; it can have broader implications for structural engineering. Understanding the effects on structures is essential for engineers:
- Hydraulic structures: These can be heavily impacted by cavitation, leading to instability.
- Foundation impacts: Vibration caused by cavitation can affect surrounding structures.
- Material selection: Engineers must consider cavitation when choosing materials exposed to high-stress hydraulic systems.
Conclusion: A Comprehensive Approach to Cavitation Management
Effective management of pump cavitation is crucial for industries reliant on auto repair, farm equipment repair, and crucial engineering practices. By understanding the fundamentals of pump cavitation, recognizing its signs, and implementing proactive strategies for prevention, businesses can enhance their machinery's reliability and operational efficiency.
As a conclusion, cavitation not only impairs equipment but also has broader implications across various engineering disciplines. By prioritizing education, proper maintenance, and adherence to design specifications, we can collectively mitigate the risks associated with pump cavitation in multiple sectors, ensuring better system performance and longevity.
Additional Resources
To further enhance your understanding of pump cavitation and its related practices, consider the following resources:
- Michael Smith Engineers - Your source for expert engineering services.
- The Pump Industry - Resources and guidelines for best practices in pump operation.
- Fluid Mechanics Society - Research and articles on fluid dynamics topics including cavitation.