The Rise of Electric Injection in Metal Fabrication
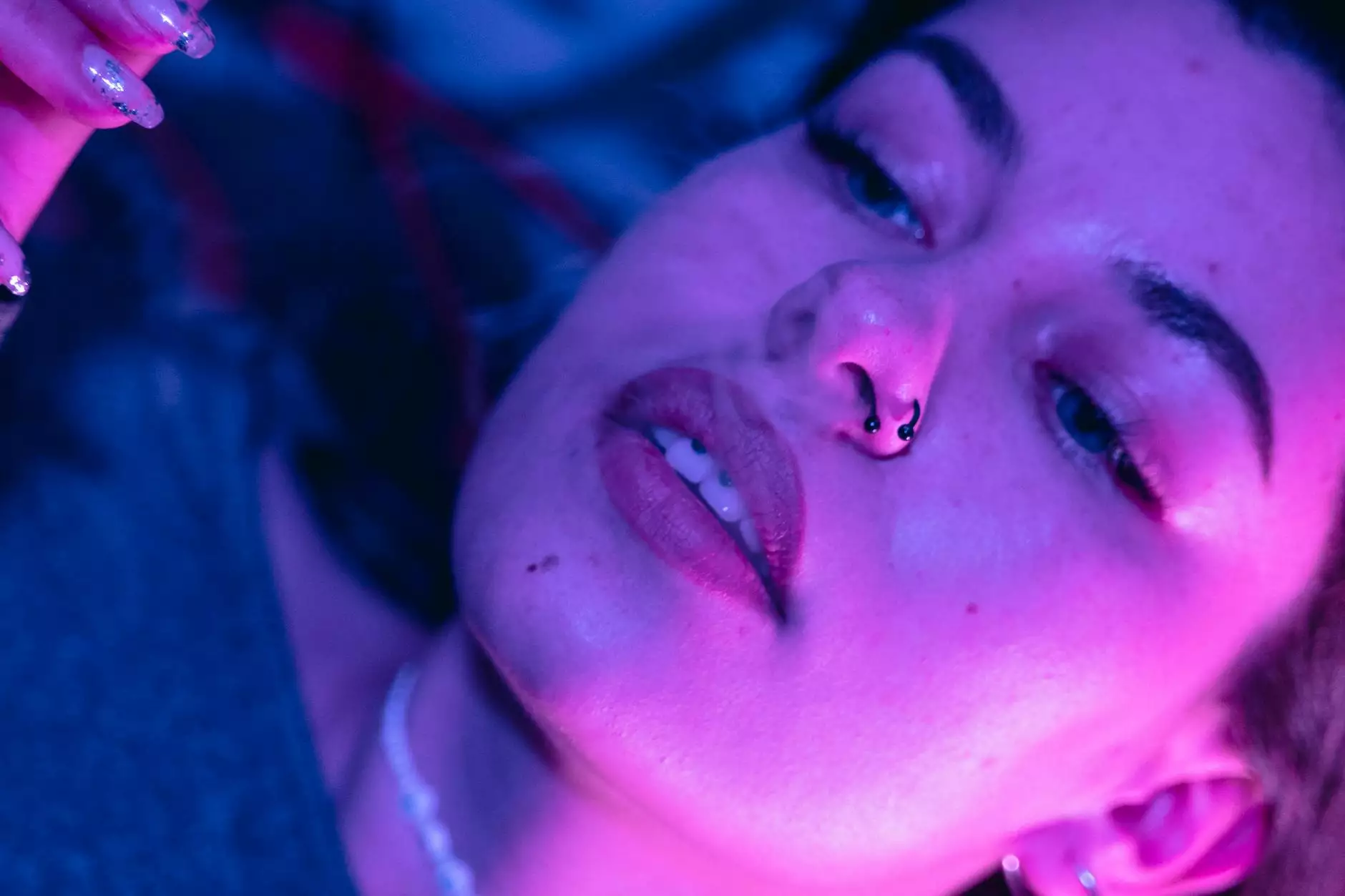
The world of metal fabrication is undergoing a transformation, and at the forefront of this change is a technology known as electric injection. As businesses strive for greater efficiency, precision, and sustainability, understanding the advantages of this innovative approach is crucial. In this comprehensive article, we delve into what electric injection is and how it is reshaping the landscape of the metal fabrication industry.
What is Electric Injection?
Electric injection refers to a cutting-edge method used primarily in the molding and shaping of metals. This technique involves the precise injection of molten metal into molds using electric-powered systems. Unlike traditional methods that rely on hydraulics or mechanical means, electric injection systems offer unparalleled accuracy and energy efficiency, making them a preferred choice among modern fabricators.
Key Components of Electric Injection Systems
- Electric Motors: Facilitate the injection process with high precision and control.
- Temperature Control Units: Ensure consistent heating of the metal, crucial for quality outcomes.
- Mold Design: Sophisticated molds designed to accommodate the specifics of electric injection technology.
- Control Systems: Advanced software allows for real-time adjustments and monitoring of the injection parameters.
Benefits of Electric Injection in Metal Fabrication
Employing electric injection in the metal fabrication process brings a multitude of benefits that can significantly enhance operational efficiency and product quality.
1. Enhanced Precision
One of the most significant advantages of electric injection is its capacity for high precision. Electric systems allow for fine-tuning of injection speed, pressure, and temperature. This level of control leads to:
- Increased dimensional accuracy.
- Minimal material waste due to better fill rates.
- Consistency in product quality, reducing the rate of defects.
2. Energy Efficiency
Electric injection systems use power more efficiently than traditional hydraulic systems. Their design minimizes energy consumption, which translates to:
- Lower operational costs.
- A smaller carbon footprint, supporting sustainability goals in manufacturing.
- Less heat generation, which reduces the need for extensive cooling systems.
3. Increased Production Speed
Thanks to their rapid cycle times, electric injection systems provide a significant boost in production speed. The advantages include:
- Faster metal cooling and solidification processes.
- Shortened manufacturing cycles, allowing for quicker time-to-market.
- Improved machine uptime due to fewer mechanical failures associated with hydraulic systems.
4. Flexible Production Capabilities
Electric injection processes can be easily adapted for various metal fabrication needs, including:
- Producing complex shapes and designs.
- Working with a wider variety of materials, including alloys that would be challenging to mold using other methods.
- Rapid prototyping and small batch productions, responding quickly to client needs.
Applications of Electric Injection in Metal Fabrication
The versatility of electric injection allows it to be utilized in various sectors of metal fabrication, particularly:
Automotive Industry
The automotive industry benefits tremendously from electric injection technology, especially in the production of lightweight components. With stringent regulations on emissions and fuel efficiency, manufacturers are turning to this method to create:
- Engine components with reduced weight.
- Durable structural parts that maintain high safety standards.
- Precision parts that enhance overall vehicle performance.
Aerospace Sector
In aerospace manufacturing, where safety and reliability are paramount, electric injection is proving invaluable for producing:
- High-strength, lightweight components that improve fuel efficiency.
- Complex shapes required for aerodynamic optimization.
- Replacement parts with tight tolerances that adhere to industry regulations.
Consumer Electronics
The production of consumer electronics also benefits from the precise and efficient nature of electric injection. Applications in this industry include:
- Enclosures that are both lightweight and durable, protecting sensitive electronic components.
- Intricate designs for mobile devices that require precision molding of small components.
- Heat dissipation parts that must conform to strict thermal management standards.
Challenges and Considerations in Implementing Electric Injection
While the benefits of electric injection are significant, businesses must also be aware of the challenges involved in implementing this technology:
1. Initial Investment Costs
Transitioning to electric injection systems often requires a hefty investment in new machinery and training for staff. However, this should be viewed in the context of long-term savings and efficiency improvements.
2. Maintenance and Technical Expertise
The complexity of electric injection systems necessitates skilled operators and maintenance personnel. Organizations need to invest in training or hiring to ensure optimal operation and upkeep of these systems.
3. compatibility with Existing Infrastructure
Integrating electric injection into a facility that already employs traditional methods may require significant adjustments to existing infrastructure, including power supplies and layout.
The Future of Electric Injection in Metal Fabrication
As technology continues to advance, the future of electric injection in metal fabrication appears promising. Emerging trends include:
1. Automation and Smart Manufacturing
The integration of Industry 4.0 technologies will further enhance the capabilities of electric injection systems, enabling:
- Real-time monitoring of production processes.
- Data-driven decisions for maximizing efficiency.
- Predictive maintenance to minimize downtime.
2. Material Advancements
As new alloys and composites are developed, electric injection will adapt to accommodate these materials, broadening its application and capabilities.
3. Sustainability Initiatives
The push for sustainable manufacturing will drive the adoption of electric injection technologies, as they align with principles of waste reduction and energy efficiency.
Conclusion
In conclusion, electric injection represents a significant advancement in the metal fabrication industry. By offering increased precision, energy efficiency, and production speed, electric injection systems empower businesses like DeepMould.net to meet modern manufacturing demands. As the industry continues to evolve, embracing this technology will not only enhance product quality but also foster a culture of innovation and sustainability in the pursuit of excellence.