The Power of Electric Moulding Machines in Metal Fabrication
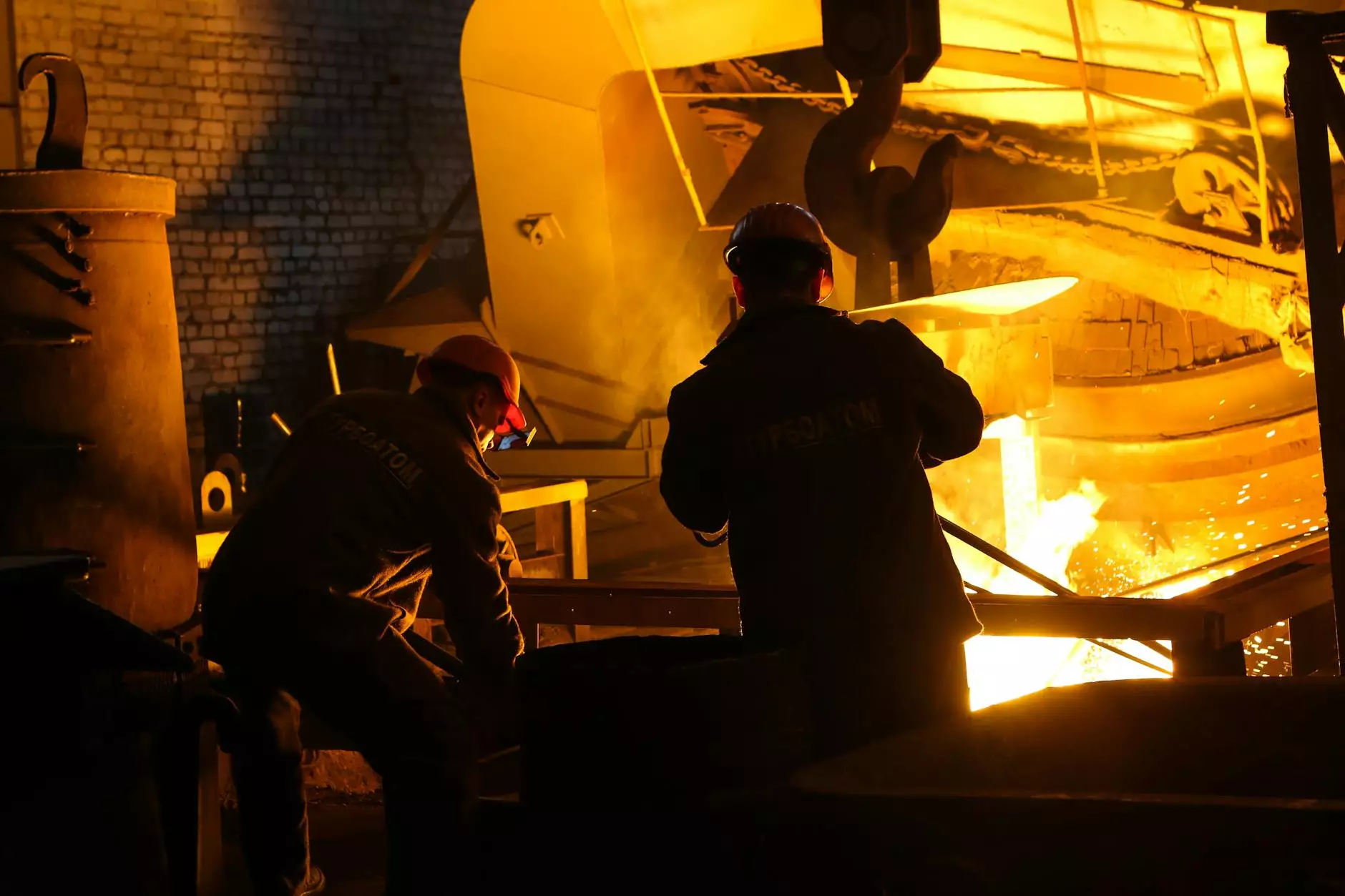
In the world of metal fabrication, efficiency and precision are paramount. One of the most significant technological advancements in this area is the introduction of the electric moulding machine. This innovative equipment has revolutionized the manufacturing process, offering a myriad of benefits that can elevate the production standards in metal fabrication. In this article, we will delve into the advantages, applications, and operational insights related to electric moulding machines.
What is an Electric Moulding Machine?
An electric moulding machine is a cutting-edge piece of equipment used primarily in the manufacturing of metal products through the process of moulding. Unlike traditional hydraulic machines, electric moulding machines rely on electric motors for operation. This significant shift not only enhances energy efficiency but also improves precision.
Advantages of Electric Moulding Machines
1. Enhanced Precision
Electronic control systems in electric moulding machines allow for highly accurate adjustments and monitoring of the production parameters. This precision results in products that meet stringent quality standards, reducing material waste and the need for secondary operations.
2. Improved Energy Efficiency
One of the most compelling advantages of electric moulding machines is their energy efficiency. These machines typically consume less power compared to their hydraulic counterparts. By using electric motors, they operate only when necessary, leading to reduced operational costs.
3. Reduced Noise Levels
Electric moulding machines generate significantly less noise during operation compared to hydraulic machines. This attribute contributes to a better working environment for employees, which can enhance productivity and reduce stress.
4. Consistent Performance
The use of electronic controls ensures that electric moulding machines operate consistently with minimal variation. This consistency is crucial for businesses that prioritize quality in their final products.
5. Lower Maintenance Costs
With fewer moving parts than traditional hydraulic systems, electric moulding machines generally have lower maintenance requirements. This leads to reduced downtime and increased operational efficiency, allowing companies to focus on production rather than repairs.
Applications of Electric Moulding Machines
Electric moulding machines are versatile and can be utilized in various applications within the metal fabrication sector:
- Automotive Industry: Used for producing interior components, frames, and other metal parts with high precision.
- Aerospace: Essential for creating lightweight yet durable components that meet strict aerospace standards.
- Consumer Goods: Facilitates the large-scale production of metal items, like kitchen appliances and tools.
- Construction: Enables the fabrication of various structural components crucial for building frameworks.
- Medical Devices: Ideal for producing precise components for medical equipment that require high levels of accuracy.
How to Optimize the Use of Electric Moulding Machines
To fully capitalize on the advantages offered by electric moulding machines, businesses should consider the following optimization strategies:
1. Regular Training for Operators
Ensuring that your operators are well-trained in the use of electric moulding machines is crucial. This training helps them understand the machine’s functionalities and maximize its potential.
2. Scheduled Maintenance
While electric moulding machines require less maintenance, it’s still vital to establish a scheduled maintenance plan. Regular inspections can help identify potential issues before they escalate.
3. Utilize Advanced Technologies
Integrating additional technologies such as automation and data monitoring systems can enhance the performance of electric moulding machines, leading to higher productivity and quality control.
4. Continuous Improvement
Encouraging a culture of continuous improvement among your workforce can lead to innovative uses of electric moulding machines, helping your business stay competitive in the ever-evolving market.
Future Trends in Electric Moulding Machines
The electric moulding machine sector is poised for continued growth and innovation. Some future trends to watch include:
1. Increased Automation
The integration of robotics and AI in electric moulding machines will further enhance efficiency. Automation will allow for more accurate, faster, and scalable manufacturing processes.
2. Sustainable Manufacturing Practices
As industries push toward more sustainable practices, electric moulding machines’ lower energy consumption will play a key role in reducing the overall carbon footprint of metal fabrication.
3. Smart Technology Integration
IoT (Internet of Things) technology will allow electric moulding machines to communicate with each other and with central systems, providing real-time data for better decision-making and efficiency.
Conclusion
The advent of electric moulding machines has truly transformed the landscape of metal fabrication. Their numerous advantages, ranging from efficiency to precision, make them an indispensable asset for modern manufacturing businesses. By embracing these innovative machines and optimizing their use, companies can not only enhance their operational effectiveness but also lead the way towards a more sustainable and productive future in metal fabrication.
For businesses aiming to take their metal fabrication processes to the next level, investing in electric moulding machines is a significant step forward. As the industry continues to evolve, those who adapt to these technological advancements will surely thrive in the competitive manufacturing environment.
For more information on electric moulding machines and how they can benefit your business, visit deepmould.net.